Automatic PET Bottle Blow Molding Machine Features:
This fully-automatic bottle blowing machine is a bottle blowing machine which is developed and researched by the most advanced bottom making technology in the current world.
Buying this blow molding machine is a fantastic investment. The machine adopts high-tech Mincro PLC controller to ensure the normal and stable operation of the machine. The preheater adopts a single-unit rotary heating design, the distance between the preheating centers is smaller, and the heating speed is faster. Compared with the old design, the dual-unit rotary heating design is adopted, which saves 30% of electricity. The special clamping system makes the clamping speed faster and saves a lot of air source at the same time.
Features.
1.Higher production efficiency, and better preform quality .
2.Special heating lamps and servo system, More energy saving.
3.Easier operation and maintenance, and 2 years free spare parts.
4.PLC, HMI and Servo system adopt Mitsubishi; Cylinder use Festo and valve use SMC; Electrical parts use Schneider; Parision controller use Moog; Hydraulic system use Yuken.
5.Higher Speed (higher output) and high productivity.
6.Ensure the delivery time and test before delivery to ensure the smooth operation of the equipment
7.Provide English manuals and video guides
New Auto Preform Unscrambler System.
*Adopts one-way preform-feeding structure and preform-separating by servo motor structure which solve the preform block and abrasion problem.
*There are two photoelectric sensors to control preform-loading motor and preform-separating cylinder that will warn the operator to add the preforms into the hopper when lacks preform instead of stopping the machine.
New Heating System.
*Perfect heating system design decrease power consumption.
*Special oven design helps power saving and easy maintain.
*Each lamp position and temperature can be adjusted.
*Cycle air-cooling system keeps the oven temperature constantly.
The Application Of Servo System On Main Transmission.
The transmission adopts servomotor for positioning that can orientate the preform-heating base quickly, accurately and steadily when the machine starts and running.
Servo Technology Innovation On Clamping System & Stretching.
*Adopts servo motor to drive the two cranks to control the clamping system which can shorten the mold-clamping time and improve productivity, and also solve the swelling mold and big joint line problem with the effect of pressurize plate.
* Servo motor using for stretching to ensure the bottle blowing speed faster and more stable bottle quality.
Specification
General Information |
|
Clamping Force | 880KN |
Clamping Stroke | 1250MM |
Max. Stretching Stroke | 350MM |
Bottom Moving Stroke | 60MM |
Number of Cavities | 6 |
Theoretical Output | 5500-6800 pcs per hour |
Max. Mould Thickness | 220MM |
Electrical System |
Voltage Standard | 380V/50HZ |
Number of Heating Zone | 9 |
Total Power (Full Loaded) | 100KW |
Container |
Max. Container Volume | 2000ML |
Neck Diameter Range | 20--40mm |
Max. Container Diameter | 110mm |
Max. Container Height | 380mm |
Air system |
Low Air compressor | 10 kg |
High Air compressor | 30 kg |
Dimension & Weight |
Blow molding machine | 5.6*2.3*2.2m |
Preform Autoloader | 2.5*1.8*3.7m |
Net Weight | 5.5T |
Machine photo
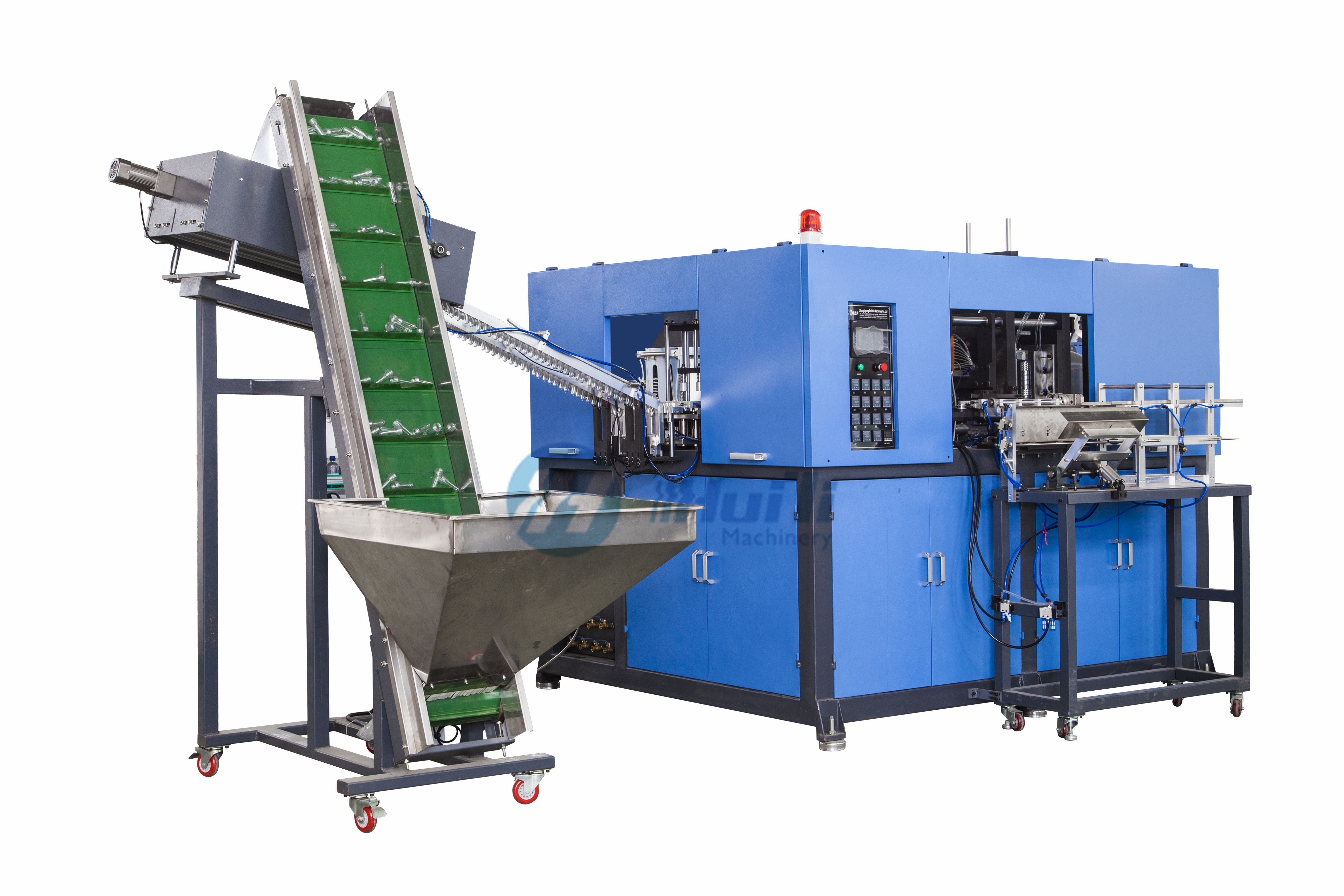